The right choice of tooling material can save you up to 40 % of your production costs. In our blogpost, you'll get to know why copper-based alloys are superior to conventional tool steel in injection molding.
The cycle time is a crucial factor in injection molding in the plastic industry. The longer the cycle, the higher the total costs associated with producing finished parts. A few seconds may not make a big difference at first glance, but when millions of parts have to be produced, every second that can be gained by a shorter cycle time plays a big role. Many pennies make a dollar, as the saying goes. But what can you do in order to keep the cycle time as low as possible and therefore increase the process productivity?
How does thermal conductivity work?
Well, one element that plays a huge role in keeping a low cycle time, heat. It is important to know, that each material has its own thermal conductivity, which determines the ability to transfer heat from a hot object to a cold object. Because of their unique structure, metals are great heat conductors. The free electrons in their structure ensure that metals have a very good thermal conductivity.
When it comes to injection molding, one thing you want to achieve is to cool down the molten plastic as quickly as possible. On one hand, this increases your productivity. On the other hand, it also increases the quality of the manufactured product as with an increased cooling time, the risk of shrinkage increases too.
Why high conductivity copper alloys are important
Especially if the finished machined parts need to suit accurate dimensions with very tight tolerances, it becomes important, that the molten plastic solidifies rapidly. This is where typical tooling materials such as tool steels or even high thermal conductivity steels (HTCS) reach their limits and manufacturer consider some alternative tooling materials in order to build the mold.
Due to their outstanding thermal conductivity, copper-based alloys such as AMPCOLOY® are ideally suited to dissipate the heat as quickly as possible. On one hand, these copper alloys can form the entire core of the mold. On the other hand, they can also be used in the places of the mold where they are specifically needed.
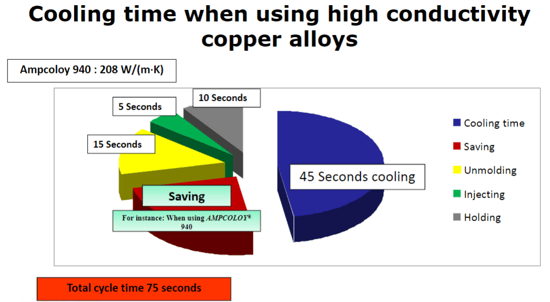
Why AMPCO?
Conventional tool steel reaches its limits quite quickly. Be it due to limited thermal conductivity, due to limits of the design and feasibility, or its fundamental physical limits. For instance, products that are fabricated with tool steel may have sink marks due to shrinkage of the plastic, as the cooling time was too long.
This is where the outstanding alloys of AMPCO METAL offer great advantages. While tool steel provides a thermal conductivity of approximately 20 W/mK, the thermal conductivity of AMPCOLOY® 940 is ten times higher! Therefore, AMPCOLOY® offers optimal cooling with effective heat removal. Furthermore, the cycling time is reduced which leads to a significant increase in productivity and ultimately in profitability too. With optimal mold cooling, companies have the potential for savings of between 10 % – 40 %.
You want to know more about the metallurgy of copper and copper-based alloys? Download now a free extract of our book «Metallurgy of Copper and Copper Alloys»