Molds for sand casting live a short life. Yet they play a crucial role in the industry as roughly 60% of metal castings are produced by sand casting. Learn in this blogpost about the best choice of molding material.
Casting is a manufacturing process with a great history. Already almost 6,000 years ago, humans casted simple jewelry, tools, and many other things.
Today, we use casting to manufacture highly complex parts, but the basic principle has always remained the same: molten metal is poured into a prefabricated mold resulting in a predesigned shape after solidification. These prefabricated molds often don’t get the recognition they deserve. This blogpost sheds a light on the mold production for sand casting. As this is a highly complex four-step process, we'll discuss each step in a separate blogpost starting with the first step of the production which is the preparation of the molding material.
The importance of the right type of sand
To meet the high demands of sand casting, a special type of sand for the mold production is required. So-called raw sand is used for the mold because it mostly contains quartz, which has a high melting point of 1713 ° Celsius and a high hardness. These characteristics make raw sand well suited for casting thanks to its high wear resistance and high temperature resistance. When selecting raw sand, the amount of quartz should be as high as possible.
But there is more to it. The grain shape and surface smoothness also play an important role. The grains should be round and its surface as smooth as possible. Thus less resin is required later on. Moreover, cavities on the surface of the sand would make the sand brittle – a rather undesirable characteristic for a mold.
Increased water content in the sand also makes the sand brittle. Therefore, the raw sand should always be dried, so that the water content is lower than 0.2%. Another key element to keep an eye on is the pH value, which has a decisive influence on the hardening speed and the final strength of the resin sand. Typically, the pH value of sand lies between 6.5 – 7.2.
The ratio of the molding materials is key
Furan resin is added to the sand as a bonding agent. The higher the content of furfuryl alcohol in the furan resin, the higher the strength - the mold is, therefore, less brittle. It has also a positive influence on the thermal strength of furan sand. A furfuryl alcohol content of 70 – 80% is ideal to achieve a good level of strength at room temperature.
The content of nitrogen has to be in a specific range as well, otherwise the furan resin becomes brittle. Low nitrogen content is desirable, but if the content is lower than 1%, the furan resin loses much of its strength at room temperature.
The choice of the right curing agent
The last component for the self-curing furan resin sand is a curing agent. Acids are generally very well suited for this purpose. A distinction is made between organic and inorganic acids. However, inorganic acids are not well suited as a curing agent because phosphoric acid stores water in the sand, and sulphuric acid is highly corrosive. For this reason, organic acids such as P-toluene sulfonic acid or xylene flavic acid are more commonly used.
As you may have noticed by now – producing a mold for sand casting is much harder than you might have thought. At AMPCO METAL we have mastered this process for decades. Our clients benefit from this great experience in mold production and enjoy the high quality of our end products. Read in our next blogpost how to set up a suitable casting process design.
If you want to dive deeper into the world of copper and copper alloys, download a free extract of our book "Metallurgy of Copper and Copper Alloys". It is a compilation of metallurgical work made on copper and copper alloys that has been produced in collaboration with metallurgy expert Piet Wenschot.
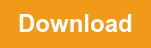