Acid environments are particularly harmful to metals. Among other things, they accelerate corrosion. Materials used in these environments have to be very resistant and withstand a lot. This is why Aluminum Bronze is often used in this context.
First of all, we need to specify exactly what acid environments are and where they occur. An acidic environment is an area with a pH value below 7.0. The lower the pH value, the more acidic the environment. Such acid environments can be found anywhere in the world - either naturally or caused by humans. In nature, these acidic environments occur mainly at hydrothermal sites in the deep sea or on land, in oil and gas or in sulphate soils. Man-made acid environments include mining areas with their landfills and mine drainage.
Acidic environments generate corrosion
Materials that come into contact with acidic liquids or gases corrode more quickly. Such acid environments are particularly harmful to materials because the concentration of hydrogen ions increases the more acidic an environment is. These hydrogen ions are responsible for acid corrosion. The lower the pH value of a liquid, the higher the corrosion rate. Corrosion therefore occurs more frequently in strong acids. Metals used in such environments must be field proven and be particularly corrosion-resistant.
Pipelines are a typical example of such an environment. Liquids containing water with a low pH value flowing through such pipes can intensify the corrosion process on the material. It is therefore important that such pipelines are made of corrosion-resistant materials so that their functionality is maintained with as little maintenance as possible. A metal that is ideally suited for this purpose is Aluminum Bronze.
Another such environment is the potash industry. The term "potash" refers to a group of potassium bearing minerals and chemicals. The compound potassium chloride is a dominant element and has a very corrosive effect on nearly any material – except the AMPCO-alloys. Potassium chloride has a pH value of less than 1 and is therefore very acidic. Indeed, the pH is so low that in combination with water and, even condensed water, it creates a very severe corrosion environment. In combination with high temperatures the corrosion rates can reach several mm/year.
A special copper alloy
All alloys with a copper content of at least 60 % are usually referred as bronze. There are various types of bronze, all named after the metal that is mainly added to copper. For example, there are beryllium bronze, manganese bronze - or the above mentioned Aluminum Bronze. This special type of bronze is a golden-yellowish copper alloy to which aluminum is added. The aluminum content is usually between 9 and 14 percent. Often other alloying elements such as iron, manganese or nickel are added in order to further promote certain properties of the metal.
The alloy can be produced in a wide variety of production method: sand, centrifugal and shell-mold castings, forgings, rolled sheets and plates, extruded and continuous-cast rods or tubes. It is used in the aviation industry, mechanical engineering, the steel industry, the marine industry, and the oil and gas, among others. They are also highly suitable for the use in acid environments.
Aluminum Bronze is ideal for acidic environments
Acid solutions lead to a relatively fast corrosion of many alloys. Not so with Aluminum Bronzes. This material is almost unaffected by the non-oxidizing acids. Aluminum Bronze is therefore characterized by its resistance to corrosion. They are resistant to seawater, scaling, sour environment, erosion and cavitation, among others. They are wear-resistant and heat-resistant up to approximately 400° Celsius. These properties make the metal particularly suitable for use in sulphuric acid, hydrochloric acid or acetic acid.
The specialized products of AMPCO®
Due to their acid resistance, AMPCO® alloys are ideally suited for the use in acid environments. Above all, they have a very high corrosion resistance to diluted sulphuric acid. AMPCO's Aluminum Bronzes also outperform conventional materials when in contact with undiluted hydrochloric acid or with agglomeration of acid sludges. In contact with many other acids, such as phosphoric acid, acetic acid, formic acid, hydrofluoric acid and propionic acid, it also proves its outstanding acid and corrosion resistance.
One of the reasons why AMPCO®8 is used regularly in the potash industry is because of these properties. Stringent manufacturing procedures, severe quality controls and precise chemical composition make AMPCO alloys resistant where other material badly fail.
Download the Technical Paper «The advantages of Aluminum Bronze in corrosive environments» for free!
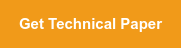